螺旋上料机在化工、食品、环保等领域广泛应用,但输送粘性物料(如污泥、糖浆、湿黏性粉末)时,常因物料粘连或堆积导致堵塞,严重影响生产效率。本文结合设备设计与操作实践,从内壁防粘涂层和螺旋角度调整两方面提出系统性解决方案,助力企业提升设备运行稳定性。
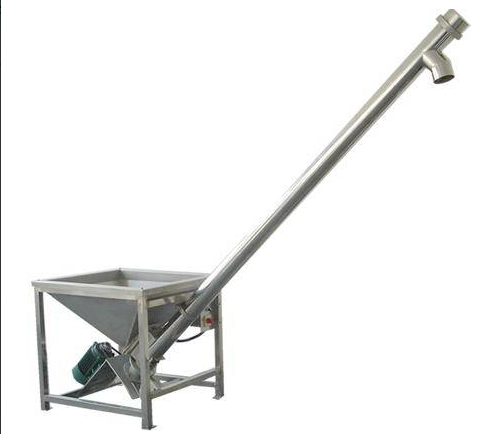
一、粘性物料堵塞的成因分析
物料特性影响
高粘性物料易附着在螺旋叶片或内壁上,形成“结块效应”,导致输送阻力增大甚至完全堵塞。若物料湿度较高(如含水率>15%),还会因摩擦阻力增加加剧堵塞风险。设备设计缺陷
- 内壁粗糙:普通碳钢材质易残留物料,长期积累形成堵塞源。
- 螺旋角度不当:倾斜角度超过20°时,物料重力分力增大,输送效率显著降低。
- 轴承结构问题:中间悬挂轴承横向尺寸过大,易阻碍物料流动。
二、核心解决方案:内壁防粘涂层+螺旋角度优化
(一)内壁防粘涂层技术
涂层材料选择
- 不锈钢内壁抛光:与物料接触部分采用304/316不锈钢材质,焊接口抛光至Ra≤0.8μm,减少附着点。
- 特氟龙(PTFE)涂层:耐腐蚀且摩擦系数低(≤0.04),尤其适用于含糖、油脂的粘性物料。
- 陶瓷复合涂层:通过等离子喷涂工艺形成耐磨层,适用于含硬质颗粒的粘性物料(如矿渣浆)。
涂层工艺要点
- 预处理:喷砂除锈至Sa2.5级,确保基材表面清洁度。
- 厚度控制:单层涂层厚度50-100μm,多层叠加需间隔固化时间。
- 边缘强化:螺旋叶片与内壁接触区域增加50%涂层厚度,防止刮擦脱落。
(二)螺旋角度与结构优化
角度调整原则
- 水平输送段:保持角度≤15°,确保物料匀速推进。
- 倾斜输送段:分段设计,每段倾斜角不超过20°,长距离输送时增设中间支撑轴承。
螺旋结构改进
- 无轴螺旋设计:取消中心轴,避免粘性物料缠绕,输送效率提升30%以上(适用于污泥、厨余垃圾)。
- 变螺距叶片:进料端采用小螺距(100-150mm)增强推送力,出料端增大螺距(200-300mm)降低阻力。
- 反旋向叶片:在出料口加装10-20cm反向叶片,利用离心力破除端部物料堆积。
配套参数匹配
- 转速控制:粘性物料输送时转速应≤60rpm,防止物料升温结焦。
- 功率适配:根据物料堆积密度(如污泥密度1.2-1.5t/m³)选择电机功率,避免超负荷运行。
三、辅助防堵措施
智能监测系统
- 在料仓安装光电料位传感器,实时监控物料高度。
- 出料口设置堵塞感应器,触发报警后自动启动反转排料功能。
机械辅助装置
- 振动破拱器:在料仓侧壁安装气动锤或电动振动器,频率设定为10-15Hz,防止物料架桥。
- 可拆卸防堵活门:卸料端盖板开设活门,堵塞时物料压力顶开活门并联动停机。
操作规范
- 严格遵循“空载启动、空载停机”流程,避免残留物料硬化。
- 定期清理螺旋管底部清料口,防止杂质积累(建议每班次清理一次)。
四、实际应用案例
某食品厂输送含糖浆物料时,原设备每小时堵塞2-3次。改造措施包括:
- 内壁喷涂0.1mm特氟龙涂层;
- 螺旋角度从25°调整为18°,并加装反向叶片;
- 电机转速从90rpm降至50rpm。
改造后连续运行72小时无堵塞,输送效率提升40%。
五、总结
粘性物料堵塞问题的解决需综合材料科学与机械设计:内壁防粘涂层降低附着阻力,螺旋角度优化改善受力分布,辅以智能监测与规范操作,可显著提升设备可靠性。企业应根据物料特性(如粘度、湿度)定制化选择方案,并定期维护以延长设备寿命