在工业生产中,螺旋上料机和螺旋提升机是物料输送系统的核心设备,广泛应用于食品、化工、矿业等领域。然而,在低温环境下(如-20℃以下),这类设备的启动困难问题尤为突出,直接影响生产效率和设备寿命。本文将从低温环境对设备的影响、电伴热系统的配置方案及能耗对比三个方面展开分析,为工程实践提供参考。
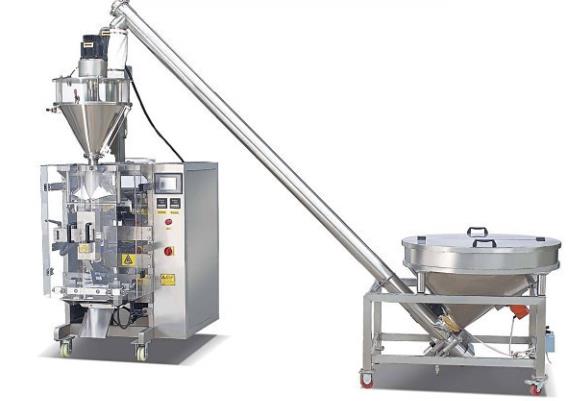
一、低温环境对螺旋上料机运行的影响
螺旋上料机通过电机驱动螺旋叶片旋转实现物料输送,其核心部件包括驱动电机、减速机、螺旋轴及密封结构。在低温环境下,这些部件会面临多重挑战:
润滑油黏度增加:低温导致润滑油脂凝固,增大电机启动阻力,甚至引发电机过载烧毁 。
钢材冷脆现象:设备钢结构在-20℃以下易发生脆性断裂,尤其是焊接部位和应力集中区域,可能引发机械故障 。
物料流动性下降:输送粉状或颗粒物料时,低温可能使物料结块,增加螺旋叶片的摩擦阻力,导致堵料或叶片磨损。
电气系统性能衰减:传感器、控制电路等电子元件在低温下响应延迟,影响自动化控制精度 。
以某铝业公司的螺旋提升机为例,其在150℃高温环境下运行稳定,但在冬季-15℃时频繁出现启动失败,需空载预热30分钟以上才能正常投料 。这表明低温环境对设备的适应性提出了更高要求。
二、电伴热系统的配置方案
为应对低温挑战,电伴热系统成为螺旋上料机和螺旋提升机的重要解决方案。其原理是通过电阻加热或自控温伴热带,对设备关键部位进行局部保温,具体配置需考虑以下因素:
伴热区域选择:
电机与减速机:缠绕伴热带以维持润滑油脂流动性,避免冷启动磨损。
螺旋输送管:沿管道外壁敷设伴热带,防止物料结块黏附。
电气控制柜:内置恒温装置,保障电子元件稳定运行 。
伴热功率计算:需根据环境温度、设备散热面积及目标维持温度综合设计。例如,某食品厂为螺旋提升机配置了15W/m的伴热带,将输送管表面温度维持在5℃以上,能耗较传统热风加热降低40%。
智能控制策略:采用温度传感器与PLC联动,实现“按需加热”。例如,在非生产时段降低伴热功率,仅维持基础保温,进一步优化能耗。
三、电伴热与其他加热方式的能耗对比
为评估电伴热系统的经济性,需对比其与传统加热方式的能耗差异:
加热方式 | 能耗(kW·h/天) | 维护成本 | 适用场景 |
---|---|---|---|
电伴热系统 | 20-30 | 低 | 长期运行、精准控温需求 |
蒸汽伴热 | 50-70 | 中 | 高温物料同步加热 |
热风循环 | 80-100 | 高 | 短期应急使用 |
保温材料包裹 | 5-10(被动) | 极低 | 辅助节能措施 |
以某化工厂的螺旋上料机为例,电伴热系统年耗电量约为1.1万kW·h,而蒸汽伴热需2.8万kW·h,且后者还需额外维护管道阀门。可见,电伴热在长期运行中更具优势,尤其适合对能耗敏感的企业。
四、应用建议与未来展望
设备选型优化:在低温地区优先选择耐寒设计的螺旋提升机,如采用低温钢材质、集成预加热模块的设备 。
系统集成设计:将电伴热与设备控制系统深度融合,实现能耗与性能的动态平衡。
定期维护检测:冬季前需检查伴热带绝缘性能,清理螺旋叶片积料,避免冷启动过载 。
未来,随着自限温材料和光伏储能的普及,电伴热系统的能效比有望进一步提升,为螺旋上料机在极端环境下的应用开辟更广阔空间。
结语
低温环境下螺旋上料机和螺旋提升机的启动难题,可通过科学配置电伴热系统有效缓解。相比传统加热方式,电伴热在能耗、维护成本和控温精度上表现突出,是企业实现低温高效生产的优选方案。随着技术进步,这一领域将持续推动工业设备向更智能、更节能的方向发展。